How are discovered product quality issues handled?
- Share
- Issue Time
- Sep 11,2024
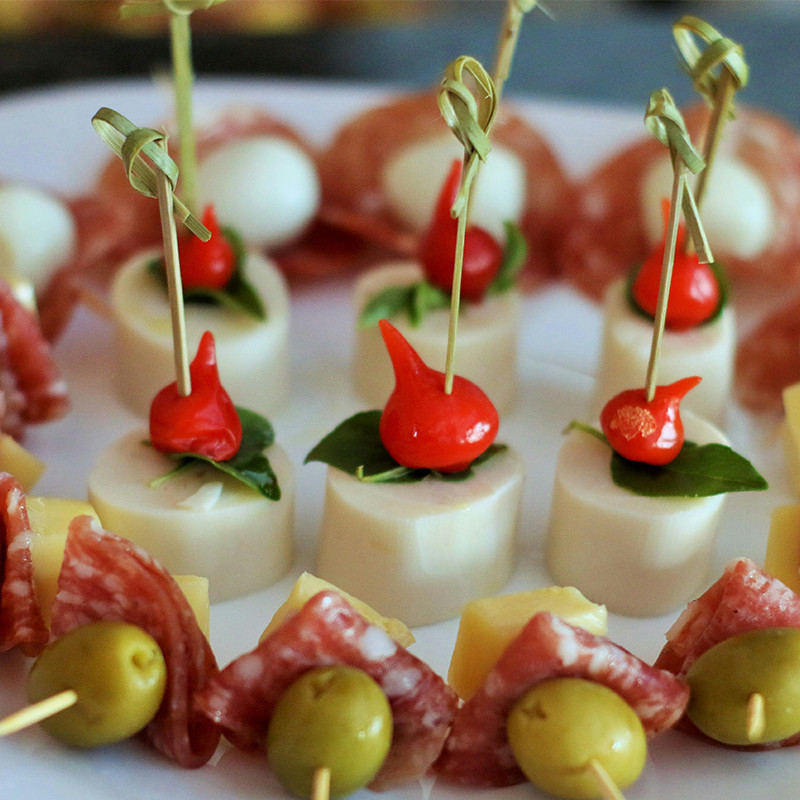
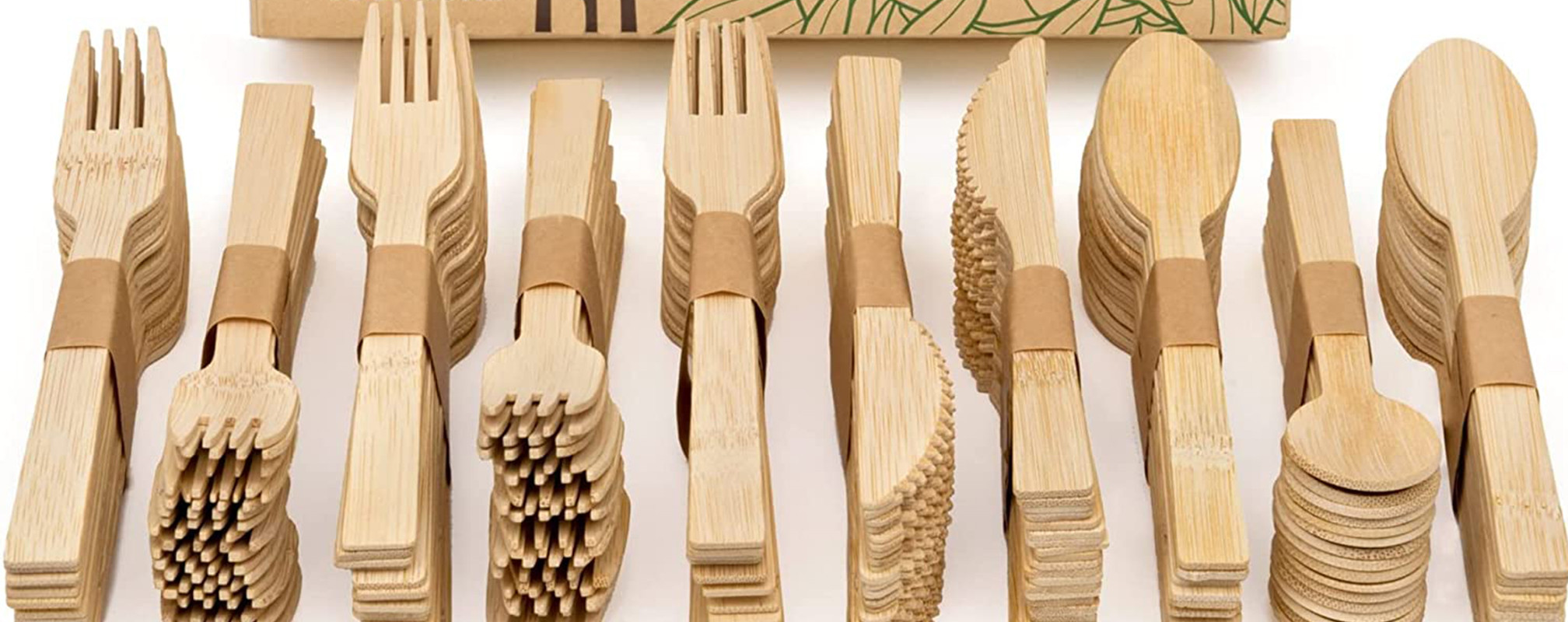
Upon discovery of any quality issues during the production process or through final quality inspections, QL immediately implements a series of stringent measures to address these concerns.
Firstly, the affected batch of products is isolated immediately to prevent the distribution of defective items into the market. Subsequently, a specialized quality control team conducts a thorough assessment of the defective products to determine the cause and extent of the defects. This assessment may involve reviews of product design, raw materials, production processes, and compliance with operational standards by personnel. Once the root cause of the issue is identified, the company swiftly executes corrective actions, which may include adjusting production processes, changing raw material suppliers, enhancing operator training, or updating equipment.
Additionally, to ensure the effectiveness of these measures, the company conducts subsequent product tests to verify whether the improvements meet the expected outcomes. Through this systematic approach, the company can respond quickly and resolve quality issues, ensuring that product quality meets the high standards of both the company and its customers. This not only helps maintain the company's brand reputation but also enhances overall production efficiency and product quality through continuous improvement.