How does QL handle non-conforming products?
- Share
- Issue Time
- Sep 11,2024
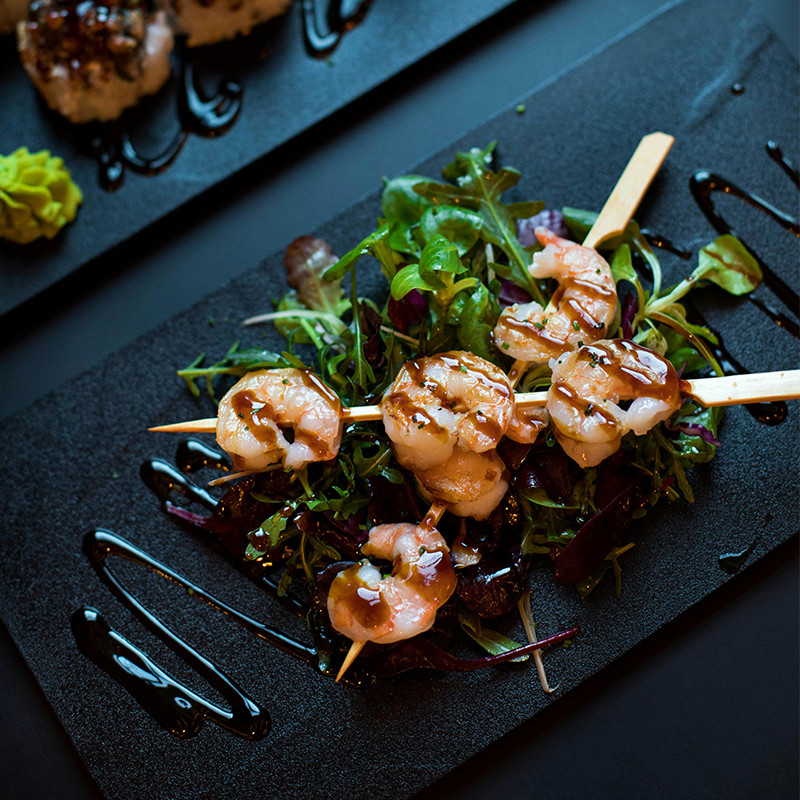
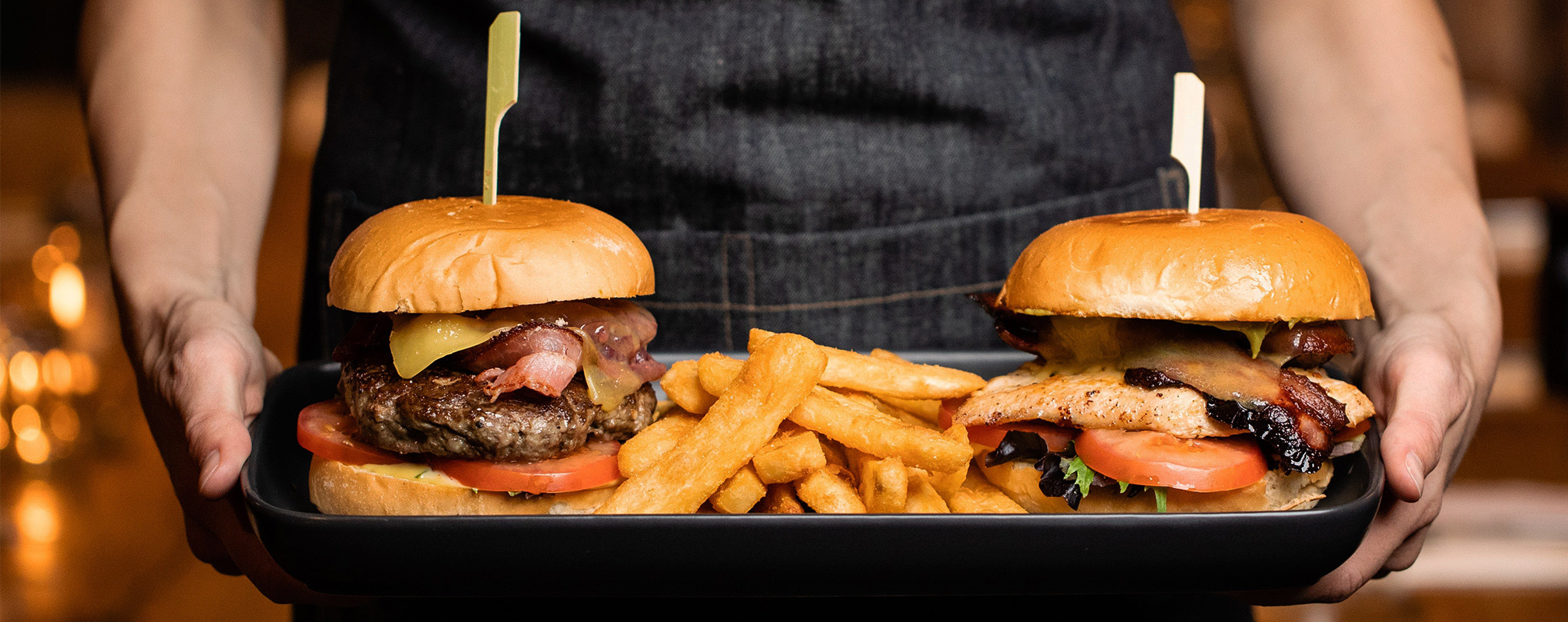
At QL, all identified non-conforming products are immediately marked and strictly segregated to prevent any mix-up with conforming items. The process for handling non-conforming products is very clear to ensure no negative impact on customer interests.
Firstly, the quality control team conducts a detailed analysis of the non-conforming products to determine the nature and cause of the issues. Based on the results of this analysis, the company decides whether to rework these products to meet quality standards or to scrap them. If reworking is chosen, it is done under strict quality control to ensure the issues are thoroughly resolved. If the decision is to scrap, these non-conforming products are disposed of in an environmentally friendly manner, ensuring compliance with all applicable environmental regulations.
Additionally, the company records and tracks all cases of non-conforming products as part of its continuous improvement program to reduce the occurrence of similar issues in future production. This rigorous process for handling non-conforming products not only protects customer rights but also reflects the company's commitment and responsibility towards product quality.